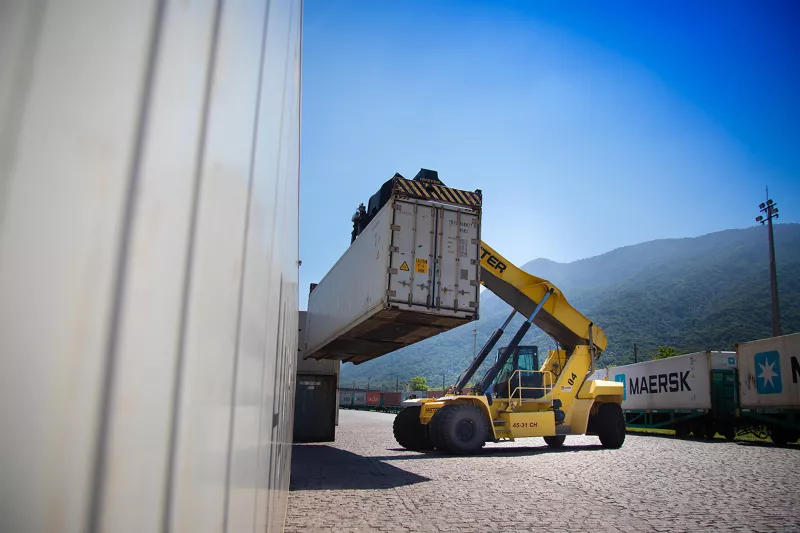
The sound of change.
Logistics terminal modernizes facilities by replacing 30 analog horn speakers with eight Axis IP horn speakers, at an initial purchase cost that is one-quarter the price of the older system with reduced maintenance costs.
Mission
The Cesari Group includes eight companies operating in chemical shipping and handling, product storage terminals, fertilizer processing, and shipping container cleaning and maintenance. One of its companies is Terminal Logístico Cesari (Terloc), which handles entry and exit control and loading/unloading all raw materials and finished products from one of the Group’s plants.
Terloc’s Base 1, located in the Cubatão Industrial Park in São Paulo, decided to improve its services by replacing its old analog communication system of microphones, amplifiers, transformers, and fiberglass horn speakers— and their associated high maintenance costs—with a VOIP system. The truck parking facility needed a modernized communication system to provide drivers with guidance on cargo movement.
Solution
The company partnered with Sillis, a specialist in communications and electronic security projects. Sillis provided Terloc with equipment on loan to test out its capabilities. After demonstrating its power and integrative capacity, Sillis supplied the Axis network products that would make up the terminal’s new IP communication system, particularly AXIS C1310-E and AXIS C3003-E Network Horn Speakers. Thanks to their SIP protocol, it was possible to integrate the horn speakers into the company’s PABX system. In addition to the horn speakers, the project also included AXIS C2005 Network Ceiling Speakers and AXIS C1004-E Network Cabinet Speakers.
Result
The first project phase to be delivered was the replacement of the 30 analog horn speakers (which had initially cost more than USD 35K) with eight Axis IP horn speakers (at one-quarter the cost of the old system). The savings allowed for the purchase of an additional eight horn speakers for use in other areas, in addition to the other IP speaker models. All communications at the two Base 1 yards are now handled via PABX: all you need to do is enter the vehicle identification number. A third yard has also been modernized. The plan is to expand this technology to other branches of the group in the rest of São Paulo state.
Our managers’ challenge was to modernize the communication system and bring it into the world of information technology. With Axis equipment, we created another level of communication for the company using PABX.
Flexible, open solution meets growing needs
When the project started, nobody knew what the best equipment would be. But the guiding principle was SIP technology. Faced with this challenge, Javas Prata, an IT analyst for Grupo Cesari, did field research until he found Sillis and its Axis solutions. “Our technical team knew about the compatibility of SIP technology with PABX extensions, but the equipment was the missing link. In that respect, the two companies were of fundamental importance. Sillis let us borrow a system for testing and stood by our side during the initial installations, supporting us in every possible way. The field-testing phase was critical to obtaining approval from the board to move forward with the project,” he said.
The work started by installing eight horn speakers (AXIS C3003-E) at the Base 1 branch in Cubatão, in the state of São Paulo. After the success of the first phase, two new phases were completed. After that, four additional audio devices—this time using AXIS C1310-E Network Horn Speakers—were installed at Cefertil, another group company.
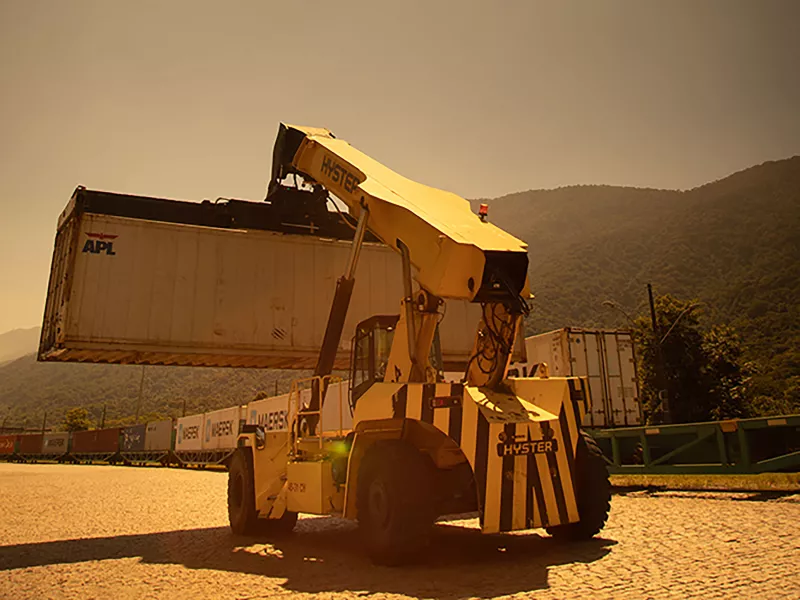
The smart choice
Javas knew that analog audio systems could be expensive at the time of purchase and in terms of ongoing maintenance. Their previous system needed 30 speakers with an initial cost of USD 35K. The price of maintenance needed for so much equipment drove the final cost even higher.
“Due to the high cost of maintaining the analog system, we chose to look for something simpler for the Terloc technology team to manage and maintain,” Javas explained. The decision proved to be a smart one. “Using the VOIP system, we could cover the same yard with fewer pieces of equipment, at a much lower cost than the previous system. Installing the IP devices was so easy, our in-house team was able to handle it,” said Javas. “Another advantage of an IP system is maintenance time. The old system normally required maintenance four times a year. With the Axis equipment, after almost two years of continuous daily use, only one device needed to be repaired, and we managed to restore it to perfect working order,” he says in admiration.
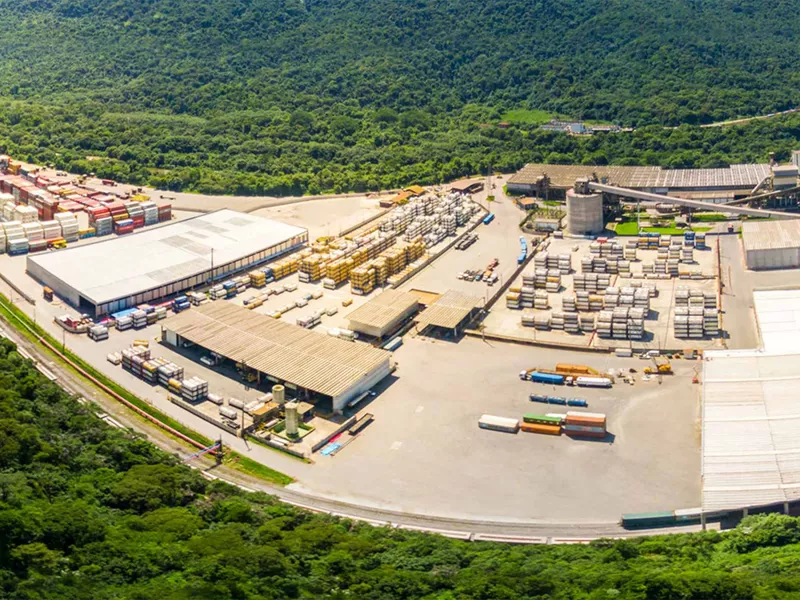
Javas emphasized that the directors prioritize the company’s modernization, and Axis’s IP systems mesh perfectly with that goal. “The sense of improved audio quality from Axis products was immediate for operators and customers. By loading its equipment with technologies such as IoT, Deep Learning and so on, Axis is right in line with the Cesari Group philosophy.”
Products & solutions
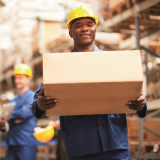
Cargo & logistics
Get in touch
Want to know how you can benefit from Axis solutions? Get in touch and we will help you.
Contact us